Summary
There are four alternate approaches to Balanced Mix Design described in AASHTO PP 105.
- Approach A requires full compliance with the existing volumetric requirements and additional performance requirements and thus, is the most conservative approach and has the lowest innovation potential.
- Approach B requires full compliance with the existing volumetric requirements at the preliminary OBC but allows moderate changes in asphalt binder content for performance optimization based on mixture performance test results. Although Approach B is slightly more flexible than Approach A, it is still considered a conservative approach with limited innovation potential.
- Approach C allows some of the volumetric requirements to be relaxed or eliminated as long as the performance criteria are satisfied. The mix design modifications that can be used in performance optimization are not limited to changes in asphalt binder content. Therefore, it is less conservative than Approach A and Approach B and provides a medium degree of innovation potential.
- Finally, Approach D has no requirement on volumetric properties and relies solely on mixture performance test results for mix design optimization, and thus, is considered the least conservative approach with the highest degree of innovation potential.
Click on the Filter buttons below for further details.
Volumetric Design with Performance Verification
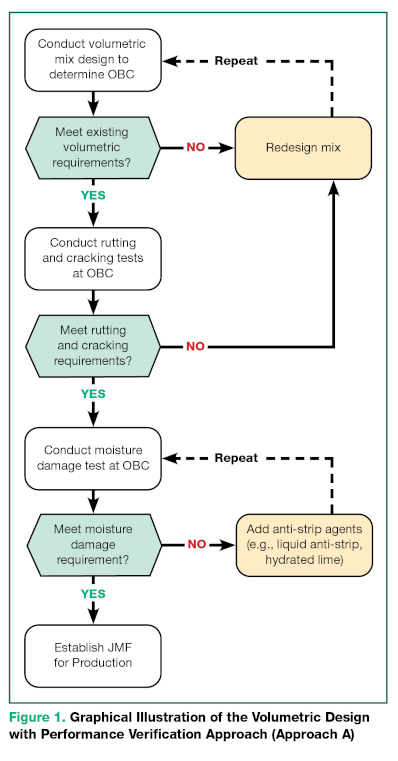
This approach starts with the current volumetric mix design method (i.e., Superpave, Marshall, or Hveem) for determining an optimum binder content (OBC) that meets all the existing volumetric requirements. Alternatively, an existing agency-approved mix design can be used. The mix design at OBC is then tested with the selected mixture rutting and cracking tests. If the mix design fails the rutting and/or cracking test criteria, the entire mix design is repeated using different materials (e.g., aggregates, asphalt binders, recycled materials, and additives) or mix proportions until all the volumetric, rutting, and cracking criteria are satisfied. After passing the rutting and cracking tests, the mix design is then evaluated with the selected moisture damage test. If the design passes the moisture test criterion, the job mix formula is established for production. Otherwise, anti-strip agents such as liquid anti-strip (LAS) additives or hydrated lime need to be added and the modified mix is re-evaluated using the same moisture damage test until a passing result is obtained. If a LAS additive is used, it may be necessary to also repeat the rutting test on the modified mix for compliance verification due to the concern that use of excessive dosage rates could soften the asphalt binder and increase the rutting potential of asphalt mixtures. Other than adding anti-strip agents, changing the asphalt binder source or aggregate type could also improve the moisture damage test result. However, these remedial modifications are not preferred because they would require the mix to be redesigned to maintain compliance with all the volumetric and performance criteria.
Volumetric Design with Performance Optimization
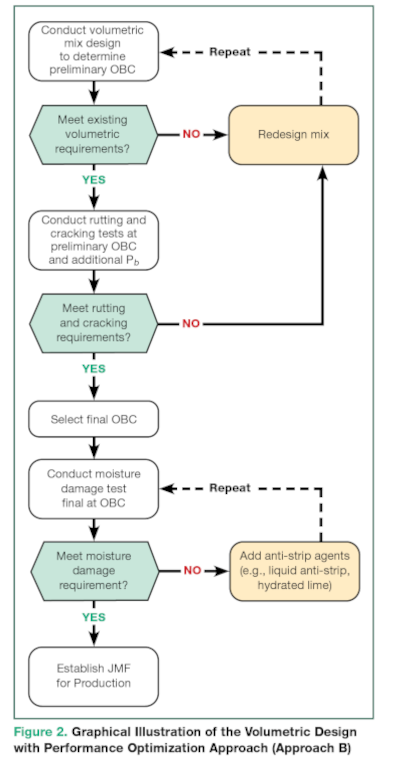
This approach is an expanded version of Approach 1. It also starts with the current volumetric mix design method (i.e., Superpave, Marshall, or Hveem) for determining a preliminary OBC that meets all the existing volumetric requirements. Alternatively, an existing agency-approved mix design can be used. The mix design is then tested with the selected mixture rutting and cracking tests at the preliminary OBC and two or more additional binder contents at intervals of ± 0.3 to 0.5 percent that bracket the preliminary OBC. Then, a binder content (not necessarily the lowest content) that satisfies both the rutting and cracking test criteria is selected as the final OBC. In cases where a passing binder content does not exist, the entire mix design process is repeated using different mix components or proportions (e.g., aggregates, asphalt binders, recycled materials, and additives) until both the rutting and cracking criteria are satisfied. After the final OBC is selected, the mix design is then evaluated with the selected moisture damage test. If the design passes the moisture test criterion, the job mix formula is established for production. Otherwise, anti-strip agents such as LAS additives or hydrated lime need to be added and the modified mix is re-evaluated using the same moisture damage test until the criterion is satisfied. Additional rutting and cracking tests could also be conducted on the modified mix for performance verification purposes.
Performance-Modified Volumetric Design
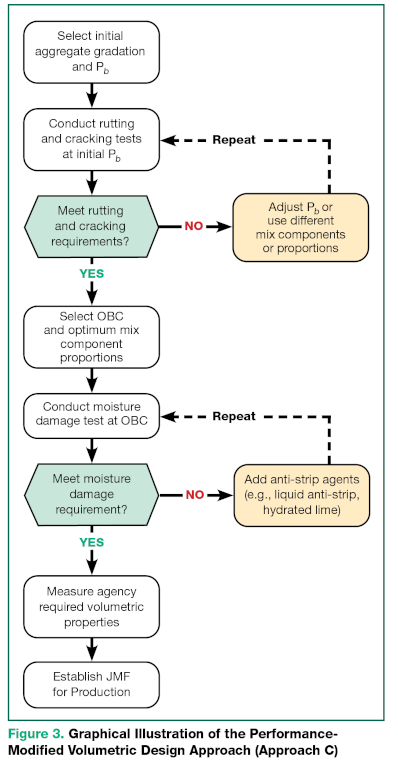
This approach starts with the current volumetric mix design method (i.e., Superpave, Marshall, or Hveem) to establish an initial aggregate gradation and binder content. Alternatively, an existing agency-approved mix design can be used. The initial design is then tested with the selected rutting and cracking tests. Test results are used to adjust either the binder content or other mix component properties and proportions (e.g., aggregates, asphalt binders, recycled materials, and additives) until both the rutting and cracking criteria are satisfied. Then, the mix design is evaluated with the selected moisture damage test. If the design passes the moisture test criterion, certain volumetric properties are measured and verified for compliance with the agency’s relaxed requirements prior to establishing the job mix formula. Otherwise, anti-strip agents such as LAS additives or hydrated lime need to be added and the modified mix is reevaluated using the same moisture damage test until the criterion is satisfied. Additional rutting and cracking tests could also be conducted on the modified mix for performance verification purposes.
Performance Design
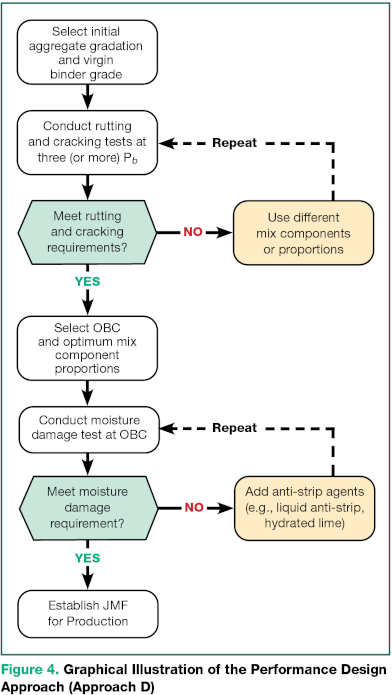
This approach starts with the selection of an initial aggregate gradation, recycled asphalt materials content, and virgin binder grade. Alternatively, an existing agency-approved mix design can be used. The initial mix design is then tested with the selected rutting and cracking tests at three or more binder contents at intervals of 0.3 to 0.5 percent. A binder content (not necessarily the lowest content) that satisfies both the rutting and cracking criteria is selected as the OBC. In cases where a passing binder content does not exist, the initial mix design needs to be adjusted using different mix components or proportions (e.g., aggregates, asphalt binders, recycled materials, and additives) until both the rutting and cracking criteria are satisfied. Then, the mix design is evaluated with the selected moisture damage test. If the design passes the moisture test criterion, the job mix design is established. Otherwise, anti-strip agents such as LAS additives or hydrated lime need to be added and the modified mix is re-evaluated using the same moisture damage test until the criterion is satisfied. Additional rutting and cracking tests could also be conducted on the modified mix for performance verification purposes.